PTS-1 controller over fuel dispensers and ATG systems
PTS-1 controller over fuel dispensers and ATG (automatic tank gauge) systems for petrol stations serves as a protocols converter. It knows communication protocols of a more than 120 brands of fuel dispensers and more than 45 brands of ATG systems and probes and allows control over any of them in exactly the same way using its own input communication protocol. POS system (cash register, payment terminal) should not matter what is the brand of fuel dispenser or ATG system connected – it simply communicates to the PTS-1 controller the same way regardless the brand of fuel dispensers and ATG systems used, PTS-1 controller undertakes all work on communication with fuel dispensers and ATG systems using their native communication protocol and takes into account all their peculiarities. This completely simplifies work for a POS system developer: by having implemented input common communication protocol of PTS-1 controller the POS becomes able to provide control over any of fuel dispensers and ATG systems supported by PTS-1 controller. PTS-1 controller itself converts input communication protocol into proprietary communication protocols of fuel dispensers and ATG systems. Thus the time required for development of POS system for petrol stations is significantly reduced.
- Purpose
- General scheme of connections
- Possibilities
- Features and benefits
- Technical characteristics
- Supported pumps communication protocols
- Supported probes and ATG systems communication protocols
- Connection to fuel dispensers
- Connection to ATG systems and probes
- Conversion between pumps protocols
- Conversion between ATG consoles and probes protocols
- Monitoring over fuel dispensers and tanks
- Multi POS systems operation
- Fuel dispensers sales data for ATG consoles for tanks reconciliation and autocalibration
- PTS-1 controller configuration utility
- Developers' API, source codes and examples
- PTS-1 controller SDK (Software Development Kit)
- Open source fully-functional application for petrol stations (C# and VB.NET)
- Open-source utility for testing and indication of all operations (C# and VB.NET)
- Open-source utility for testing and indication of all operations (Java)
- Open-source utility for testing and indication of all operations (COM-object in C, application in VB6.0)
- Open source utility for testing control over pumps and ATG systems provided (Delphi 7)
- Open source utility for testing control over pumps and ATG systems provided (Python)
- PTS Terminal - tool for debugging communication with PTS-1 controller
- Pumps software simulator
- ATG systems software simulator
- Firmware updates
- Technical support
- Frequently asked questions
- Order information
Purpose #
PTS-1 controller can be called a forecourt controller and can be used together with POS systems, cash registers, OPTs (outdoor payment terminals) and other control systems for petrol stations in order to provide control over fuel dispensers, LPG (liquified petroleum gas) dispensers, CNG (compressed natural gas) dispensers and various brands of ATG systems at petrol stations and storage depots.
PTS-1 controller is supplied with a rich set of APIs (application programming interfaces) developed under most popular programming languages and environments in order to provide comfortable and quick implementation of the PTS-1 controller into control systems for petrol stations (POS system, cash register, OPT terminal, etc).
General scheme of connections #
Possibilities #
PTS fuel pump controller can simultaneously control up to 16 fuel dispenser sides (fueling places). PTS-1 controller has 4 independent pump ports, each of them can be programmed to its own communication protocol and baud rate, thus PTS-1 controller provides communication with connected dispensers simultaneously using up to 4 various communication protocols. Each PTS-1 controller pump port can connect up to 16 fueling places maximum.
PTS-1 controller can simultaneously control up to 16 ATG probes (gauges) (separate probes or probes connected to ATG systems / consoles) that use up to 3 various communication protocols and baud rates (each of the probe ports can be adjusted to a separate communication protocol and baud rate and connect up to 16 ATG probes maximum).
PTS-1 controller allows a possibility to lead management over the same fuel dispensers from several POS systems and share ATG probes measurement values between several interconnected PTS-1 controllers. Thus, every interconnected PTS-1 controller is able to provide control over any of the connected fuel dispensers and know ATG system measurement data of every other interconnected PTS-1 controller.
PTS-1 controller supports more than 120 brands of fuel dispensers of various manufacturers, among which you can find: 2A, Actronic, Adast (Adamov Systems), Ag Walker, Agira, Angi International, Ariel, Aspro, Assytech, Astron, Azt, Baransay, Batchen, Bennett, Blue Sky, Censtar, CFT Clean Fuel, Compac, Coptron, Coritec, Datian Machines, Dem G. Spyrides, Develco, Dong Hwa Prime, Durulsan, Eaglestar, Emgaz Dragon, Epco, Esiwelma, Europump, Falcon LPG, Fornovo Gas, Fuelquip, Fuelsis, Galileo, Gaslin, Gerkon, Gilbarco, Greenfield, Hitachi, Hong Yang, IMW, Intermech, Kalvacha, Kievniigaz, Korea Ene, KPG-2, Kraus, Kwangshin, Lanfeng, LG Ene, Logitron, Maser, Meksan / Wayne SU86, Mekser, Mepsan, Midco, MM Petro (Zap), Motogaz, MS GAs, Nara, Nuova Migas, Nuovo Pignone, PEC (Gallagher Fuel Systems), Petposan, Petroequip, Petromeccanica, Petrotec, Prowalco, Pump Control, Real-Tech, RIX, Safe, Salzkotten, Sanki, Sea Bird, Shelf, Scheidt & Bachmann, Shibata, Slavutich, Somo Petro, Star, Tatsuno (Japan), Tatsuno Europe (former Benc), Tekser, Tokheim, Tokheim India, Tokico, Tominaga, Topaz, Transponder, Ucar Elektric, Unicon-TIT, Vanzetti, Wayne Dresser, Wayne Pignone, Yenen, Zcheng Genuine Machines and others.
PTS-1 controller supports more than 45 types of automatic tank gauge (ATG) systems and probes of various manufactures, among which you can find: Accu, Alisonic, Assytech, Bluesky, Dut-E, Eaglestar, Ebw, Enraf, Fafnir, Franklin Fueling, Gamicos, Gilbarco Veeder Root, Hectronic, Hong Yang, Humanentec, Incon, Labko, Mts Atg Sensors, North Falcon, Omnicomm, Omntec, Opw, Qingdao Guihe, Start Italiana, Struna, Uniprobe, Vega, Windbell and others.
PTS-1 controller is CE approved and has all corresponding test reports.
Features and benefits #
- Supports over 70 communication protocols of fuel dispensers and ATG systems. List of supported communication protocols is constantly growing. A wide range of international protocols as Wayne DART, Gilbarco 2-wire, Tokheim, Tatsuno are included. Single firmware of PTS-1 controller contains all available communication protocols for fuel dispensers and ATG systems.
- Unified approach to management over any forecourt equipment - using PTS-1 controller control over any supported fuel dispenser or ATG system is done in exactly the same way by the management system (POS system, cash register, OPT terminal, etc). PTS-1 controller has a single common communication protocol. Thus having once implemented the protocol into the management system (or its API) the management system will be able to provide control over any of the supported fuel dispensers and ATG systems in exactly the same way.
- Conversion between pumps protocols - in case if POS system already knows some open communication protocol of dispensers - then it can use PTS-1 controller for its conversion to any other pump protocols.
- Conversion between ATG consoles protocols - in case if POS system already knows some open communication protocol of ATG consoles - then it can use PTS-1 controller for its conversion to any other ATG console or probe protocols.
- Real-time control over fuel dispensers and ATG systems. PTS-1 controller provides a hardware solution for stable and reliable operation of forecourt equipment.
- Scalability - PTS-1 controller provides control over up to 16 dispenser sides, in case of necessity several PTS-1 controllers can work simutaneously.
- Possibility to provide control over same fuel dispensers from several POS systems and receive data on ATG measurements from any interconnected PTS to each POS system - PTS-1 controllers, installed near each of the POS systems, can be interconnected with each other allowing each of the POS systems to provide control over each of the connected fuel dispensers or monitor its state and to have data measurements of ATG systems connected to any of the interconnected PTS-1 controllers.
- Rich set of interface converters for connection to fuel dispensers - PTS-1 controller has output pump ports in RS-485 interface so can be directly connected to fuel dispensers with this type of interface. Other dispensers having communication interface of 2-wire current loop, 3-wire current loop, 4-wire current loop, RS-232 interface are connected to PTS-1 controller through special interface converters.
- Rich software API for developers - PTS-1 controller is supplied with full API (application programming interfaces) and open-source test applications for common programming languages and operation platforms: C, C++, C#, Delphi, Java, Python, Visual Basic, COM-object.
- "All in one" configuration tool for PTS-1 controller: one configuration utility provides configuration of its pump and probe ports, internal parameters, reads version, makes firmware updates, captures logging from any channel and makes self-diagnostics of the PTS-1 controller.
- Easy firmware updating - All new firmware updates are available for download to all existing customers. Firmware update process takes about 1 minute. Easy way to back up and restore PTS-1 controller configuration between updates.
- Logging of operation - in order to remove problematic situations of PTS-1 controller communication with any forecourt equipment logging of communication exchange without interrupting PTS-1 controller operation is available, which allows quick search and elimination of any found problems.
- Self-diagnostics of operation - easy and quick built-in diagnostics of PTS-1 controller operation: CPU, memory, RS-232 and RS-485 interfaces, DIP-switches.
- Constant software updates - PTS-1 controller firmware is constantly being improved, new protocols are being added and latest updates are always available for download to all customers.
- Support by developers for developers - 24 hours support for all customers of PTS-1 controller on any standing issues.
- Credit-card size and suits to any dimension for installation inside master systems.
Technical characteristics #
PARAMETER | VALUE |
---|---|
Power supply voltage | 12 V DC |
Current consumption | 400 mA max |
Temperature range | from -40°C to +80°C |
Weight | 120 g |
Overall dimensions | 85 x 58 x 30 mm |
Supported pumps communication protocols #
Need more protocols?
We are constantly expanding a list of supported communication protocols and forecourt equipment.
Please contact us if you are interested in other pumps or probes brands, communication protocols or control equipment not listed here.
Supported probes and ATG systems communication protocols #
Need more protocols?
We are constantly expanding a list of supported communication protocols and forecourt equipment.
Please contact us if you are interested in other pumps or probes brands, communication protocols or control equipment not listed here.
Connection to fuel dispensers #
PTS-1 controller can simultaneously control up to 16 fuel dispenser sides (fueling places). PTS-1 controller has 4 independent pump ports and each of them can be programmed to its own communication protocol and baud rate, thus PTS-1 controller provides communication with connected dispensers, simultaneously using up to 4 various communication protocols. Each PTS-1 controller pump port can connect up to 16 fueling places maximum.
Connection to ATG systems and probes #
PTS-1 controller can simultaneously control up to 16 ATG probes (gauges) (separate probes or probes connected to ATG systems/consoles) that use up to 3 various communication protocols and baud rates (each of the probe ports can be adjusted to a separate communication protocol and baud rate and connect up to 16 ATG probes maximum.
At communication to ATG consoles PTS-1 controller can be used for sending fuel dispensers sales data to consoles in order to make console provide tanks reconciliation reports and automatic tanks calibration:
Conversion between pumps protocols #
In case if POS system already knows some open communication protocol of dispensers then it can use PTS-1 controller for its conversion to any other pump protocols without any additional integration.
At this control over pumps can be done in parallel from control systems connected through pump port and PC port, PTS-1 controller internally tracks which control system locks control over dispensers:
Conversion between ATG consoles and probes protocols #
In case if POS system already knows some open communication protocols of ATG consoles then it can use PTS-1 controller for its conversion to any other ATG console or probe protocols without any additional integration.
Monitoring over fuel dispensers and tanks #
In case if there is an existing POS system already installed on the station PTS-1 controller allows to monitor operation of the fuel dispensers and tanks (and optionally to make sales when required). At this PTS-1 controller is connected between existing POS system and fuel dispensers and ATG console (tank probes), PTS-1 controller communicates with fuel dispensers and ATG console (probes) using their proprietary communication protocols and with POS system – using open communication protocols for pumps and ATG console. Monitoring system can connect to PC port of PTS-1 controller and get all data of fuel dispensers sales and tanks real time, at this it can also provide control over the dispensers when required.
Multi POS systems operation #
PTS-1 controller allows a possibility to lead management over the same fuel dispensers from several POS systems and share ATG probes measurement values between several interconnected PTS-1 controllers. Thus every interconnected PTS-1 controller is able to provide control over any of the connected fuel dispensers and know ATG system measurement data of every other interconnected PTS-1 controller.
If a necessity arises to organize several working places at petrol station (several POS systems) each of the POS systems should have its own PTS-1 controller connected. PTS-1 controllers should be interconnected with each other through a dispatcher PTS port (DISP channel on RS-485 interface) and with fuel dispensers. Thus control over each fuel dispenser at petrol station can be made from every POS system and each PTS-1 controller will know measurement data of every ATG probe connected to any of the interconnected PTS-1 controllers. During authorization of a fuel dispenser from one POS system the fuel dispenser becomes locked by PTS-1 controller of this POS system and while it is locked all other POS systems cannot control given fuel dispenser, they can only monitor its current state. When operation of given POS system is finished with given fuel dispenser, PTS-1 controller of this POS system unlocks the fuel dispenser and it becomes commonly available to all other PTS-1 controllers, which makes it possible to be controlled (locked) by any of the PTS-1 controllers connected to other POS systems.
Fuel dispensers sales data for ATG consoles for tanks reconciliation and autocalibration #
Possibilities of the PTS-1 controller allow to apply it in various ways for provision of control over forecourt equipment at petrol stations and allow its easy integration with existing POS systems and OPT terminals at petrol stations.
One of the applications is listening of communication exchange between POS system and dispensers and sending of dispensers’ transactions to the ATG console for provision of tanks’ reconciliation and automatic calibration. Most of the petrol stations with installed ATG consoles do not have this option due to POS system can not provide sending of dispensers’ transactions to the console. Installation of the PTS-1 controller between POS system and dispensers solves this problem and without any additional integration from the side of POS system.
Additionally, it is possible to apply PTS-1 controller inside the casing of the ATG console. At this a scheme of connection specified on the above image is saved, but at some extra development of the console GUI it is possible to make a completely new function of the console – provision of monitoring and control over dispensers from the console in parallel with POS system. As a result, the console becomes a common system of control, monitoring and account providing:
- connection of console to any POS system, OPT terminal for provision of control over dispensers
- possibility to connect various brands of probes, which communication protocols are not supported by the console
- transmission from PTS-1 controller to console data on sales transaction of dispensers for formation of reconciliation reports and automatic tanks calibration
- additional possibility to monitor and control fuel dispenser operation from the console display in parallel to POS system already installed at petrol station (needs update of console software)
PTS-1 controller configuration utility #
PTS-1 controller configuration utility is an open source application, which provides the following operations with PTS-1 controller:
- Configuration of pump port and probe port of PTS-1 controller
- Configuration of pump protocol, ATG, and PTS-1 controller parameters
- Provision of control over the pumps and monitoring measurement values of ATG systems like real POS system
- Saving of all PTS-1 controller configuration to file and restoring of all configuration from file
- Updating of PTS-1 controller firmware
- Logging of PTS-1 controller communication on selected channel
- Self-diagnostics of PTS-1 controller:CPU, memory, RS-232 and RS-485 interfaces, DIP-switches
- Reading of current PTS-1 controller firmware version: display of firmware date, number and supported communication protocols
- Direct connection of PTS to POS system or connection through fiscal module: possibility to configure PTS-1 controller via direct connection of PTS-1 controller to POS or connection through fiscal module
- Multilanguage support: easy addition of new languages to the utility, all languages are stored in XML-file, which is easy to edit
Developers' API, source codes and examples #
PTS-1 controller for developers is supplied together with a rich set of API (application programming interfaces) for commonly used programming languages and operation platforms:
- C and C++ - API for communication with a PTS-1 controller through a COM-port, documentation and examples of application in source codes under Windows OS and Linux operating systems
-
C#:
- open source library, which includes classes, methods and properties for communication with PTS-1 controller for provision of control over dispensers and ATG systems and configuration of PTS-1 controller
- open source PTS-1 controller configuration and testing utility
- open-source utility for testing and indication of all operations provided by the PTS-1 controller, allows to perform all operations with the PTS-1 controller
- open source fully-functional application for provision of control over up to 8 pumps and 4 ATG systems by the PTS-1 controller, allows to perform all operations with the PTS-1 controller
- Delphi - API for communication with a PTS-1 controller through a COM-port, documentation and examples of application in source codes
-
Java:
- open source library, which includes classes, methods and properties for communication with PTS-1 controller for provision of control over dispensers and ATG systems and configuration of PTS-1 controller
- open-source utility for testing and indication of all operations provided by the PTS-1 controller, allows to perform all operations with the PTS-1 controller
- Python - API for communication with a PTS-1 controller through a COM-port, documentation and examples of application in source codes
-
Visual Basic .NET:
- open source library, which includes classes, methods and properties for communication with PTS-1 controller for provision of control over dispensers and ATG systems and configuration of PTS-1 controller
- open source PTS-1 controller configuration and testing utility
- open-source utility for testing and indication of all operations provided by the PTS-1 controller, allows to perform all operations with the PTS-1 controller
- open source fully-functional application for provision of control over up to 8 pumps and 4 ATG systems by the PTS-1 controller, allows to perform all operations with the PTS-1 controller
-
COM-object for PTS-1 controller:
- open-source COM-object (written in Microsoft Visual C++ 6.0 IDE in C++ programming language) with methods and properties for communication with PTS-1 controller for provision of control over dispensers and ATG systems and configuration of PTS-1 controller
- open-source application in Microsoft Visual Basic 6.0 for testing and indication of all operations provided by the PTS-1 controller, allows to perform all operations with the PTS-1 controller
- Description of communication protocol of PTS-1 controller - describes communication parameters, message structure, commands and responses between POS management system and PTS-1 controller, typical flowchart and a diagram of interaction
PTS-1 controller SDK (Software Development Kit) #
PTS-1 controller SDK (Software Development Kit) is intended for developers of POS management software for petrol stations that want to control fuel dispensers and ATG systems from their software.
PTS-1 controller SDK includes:
Hardware:
- PTS-1 controller over fuel dispensers and ATG systems for petrol stations: 1 pcs
- Interface converter RS-232/USB with cable: 2 pcs
- Interface converter RS-485/USB with cable: 1 pcs
- Cabling
Software:
- Software simulators of prevalent fuel dispensers
- Software simulators of ATG systems (probes)
-
API for developers in various programming languages:
- C and C++
- C#
- COM-object
- Delphi
- Java
- Python
- Visual Basic 6.0
- Visual Basic .NET
- Description of communication protocol with PTS-1 controller
- "All in one" configuration utility for configuration, firmware update, logging and diagnostics of the PTS-1 controller
- PumpDemo - free contracted version of NaftaPOS software for petrol stations
- Useful utilities for debugging of communication with PTS-1 controller
PTS-1 controller SDK is required and designed for software developers for:
- Improve understanding of operating the PTS-1 controller.
- Implement the PTS-1 controller into own developed POS management system or software application for control over fuel dispensers and ATG level measurement systems for petrol stations.
- Debug own software application to correctly provide control over fuel dispensers and probes locally (on the workplace) without need to connect to real fuel dispensers and probes using software simulators of pumps and probes supplied in structure of SDK.
Software simulators of dispensers and probes
Open source fully-functional application for petrol stations (C# and VB.NET) #
Open-source utility for testing and indication of all operations (C# and VB.NET) #
Open-source utility for testing and indication of all operations (COM-object in C, application in VB6.0) #
Open source utility for testing control over pumps and ATG systems provided (Delphi 7) #
Open source utility for testing control over pumps and ATG systems provided (Python) #
Firmware updates #
PTS-1 controller firmware is constantly being improved and new communication protocols are added. New versions of PTS-1 controller firmware are available for download to customers.
Technical support #
Support team provides 24 hour help and customer assistance on any questions which may arise with PTS-1 controller. Questions are answered by experienced developers and programmers, who have sufficient knowledge and can assist with any questions regarding software development.
Frequently asked questions #
WARNING! Manufacturer guarantees reliable and stable operation of products only at compliance with below requirements. In case of absence of uninterruptible power supply or incorrect wiring of products to it any claims to malfunction of software are not accepted.
1. Requirements to power supply
The described products come into structure of control system (POS) for petrol station. Power supply of the products should be done from a separate power supply with built-in filter of radio frequency interferences and limiter of high voltage pulse interferences. Power supply should have a safety factor of 1.5.
At emergency switching off the power supply or in case of power voltage exceeding its permitted ranges the products can switch off with loss or corruption of data and possible damage of hardware and software. Power supply of all electronic blocks of POS and electronic pumpheads of dispensers, which are connected through information lines, should be made from single common uninterruptible power supply source (UPS). Connection of other devices to given UPS is strictly prohibited. UPS should be of continuous action (online) and work with double conversion with output voltage regulation. UPS should have a safety factor of 1.5. Filter of radio frequency interferences and limiter of high voltage pulse interferences should be used for feeding equipment from UPS.
Supply of electronic pumpheads of dispensers should be made from the UPS unit using 3-wires scheme with isolated neutral through dedicated two-pole breaker for each dispenser. Connection of other parts of dispenser to UPS unit (expect electronic pumpheads) is strictly prohibited.
UPS unit should be connected to a separate three-pole socket fed through the three-wire feeder (phase, neutral, ground wires) with insulated neutral from a dedicated circuit breaker of switchboard. Feeder coming from the switchboard to the socket should located not closer than 0.3 meters to other feeders. The socket should be located at a distance of not more than 1 meter away from the POS. Phase wire of the feeder should not have any other consumer, which are sources of interferences (for example motors).
For protection of POS and UPS from secondary effects of atmospheric electricity it is required to install high-voltage arresters (dischargers) at the transformer substation or on poles of power lines.
2. Requirements to grounding
In the switchboard the ground wire of feeder socket should be connected to the grounding screw, which should be connected by means of welding with a protection grounding circuit of petrol station by steel wire with a diameter of not less than 5 mm.
Protection grounding circuit of petrol station should correspond to safety requirements and be separated from the station lightning protection circuit. Distance from the nearest electrode of protection grounding circuit to electrode of lightning protection circuit must be at least 10 meters. Resistance of the protection grounding circuit should be not more than 4 Ohms and must be confirmed by the test report. Length of wires from the switchboard to the nearest electrode of protection grounding circuit should not exceed 15 meters.
3. Requirements to laying of cable communications
Laying of power and information wires to dispensers should be done in separate pipes with distance of not less than 0.3 meters between each other. For informational wires (current loops, RS-485, other interfaces) it is recommended to use shielded twisted-pair cables (recommended type – FTP CAT 5E). The cable shield must be connected to the ground connector on one side only – on the side of the dispenser.
PTS controller can simultaneously control up to 16 fuel dispenser sides (fueling places). PTS controller has 4 independent pump ports and each of them can be programmed to its own communication protocol and baud rate, thus PTS controller provides communication with connected dispensers, simultaneously using up to 4 various communication protocols. Each PTS controller pump port can connect up to 16 fueling places maximum.
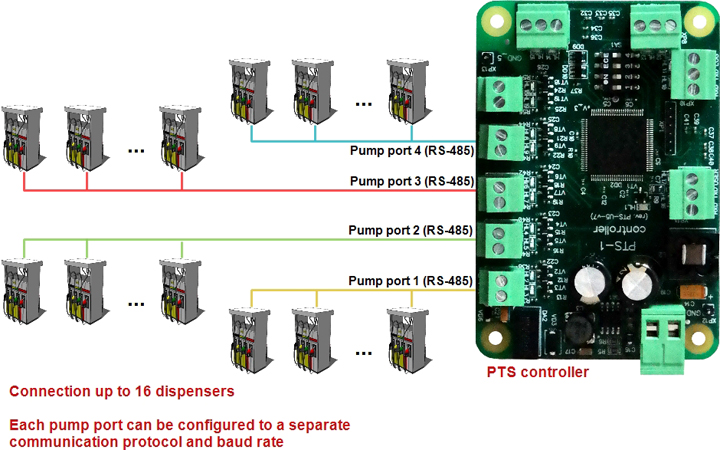
PTS controller is supplied without cables for connection to dispensers and ATG systems. For connection to dispensers and ATG systems you will have to prepare the cablings yourself. You can use any standard FTP cable with twisted pair and aliminium foil for screening (like FTP CAT 5E) for connection.
When PTS controller is to be connected directly to ATG probes installed in fuel tanks (without ATG console) - then connection should be obligatory done through the safety barrier (intrinsic safety barrier), which prevent any sparks coming from the cable in explosion dangerous area of tanks, where the ATG probes are installed.
Total quantity of pumps to be connected to PTS controller is 16. Each of the pump ports can be configured to its own communication protocol and baud rate, so you can connect dispensers of 4 various brands to the same PTS controller. You can connect up to 16 pumps to the same pump port or you can distribute all the maximum 16 pumps between the any or all pump ports. As the pump ports are working independently from each other it is recommended to distribute the connected dispensers between all the pump ports in approximately equal quantities in order to make polling of connected pumps be the fastest.
Under pump we mean a fueling place, which is a dispenser side (in case if dispenser has 2 sides) or a whole dispenser (in case if dispenser has 1 side).
The PTS controller has RS-232 interface for communication with a control system (e.g. POS system, cash register, payment terminal, etc). RS-232 interface specification allows connection with maximum distance up to 15 meters between devices using this interface. It means that the PTS controller should be used close to the control system. Interfaces normally used in dispensers allow much longer distances for communication (for example RS-485 or current loop interface normally allows distances up to 1200 meters for communication).
This depends on the type of interface used in the dispensers.
Dispensers, which use RS-485 interface, are directly connected to the PTS controller. Examples of such dispensers are: Wayne Dresser Europe, Nuovo Pignone, Wayne Pignone, Tatsuno Japan, Tatsuno Europe, Tatsuno Rus, Tokico, Bennett, Adast, MM Petro ZAP, Galileo, Develco, Safe, Wayne Meksan, Mekser, Mepsan, 2A, Petrolmeccanica, EuroPump, Sanki, Korea EnE, LG EnE, SOMO Petro, Blue Sky, Dong Hwa Prime, EPCO, Slavutich, Shelf, UniCon, UniGaz, others.
Electronic dispensers, which use 2-wire current loop interface are connected to the PTS controller through the GB interface converter. Examples of such dispensers are: Gilbarco, Tankanlagen Salzkotten, Batchen Email, Kraus, Prowalco, Wayne Dresser (USCL communication protocol), PetroTec, EuroPump, Mekser, Meksan, Petposan, PEC (Gallagher Fuel Systems), Bennett, Falcon LPG, Greenfield, others.
Electronic dispensers, which use 3-wire passive current loop interface are connected to the PTS controller through the TH interface converter. Examples of such dispensers are: Tokheim, Satam, Emgaz Dragon, Kalvacha, others.
Electronic dispensers, which use 3-wire active current loop interface are connected to the PTS controller through the LP interface converter. Examples of such dispensers are: Logitron, Emgaz Dragon, Gilbarco Marconi, others.
Electronic dispensers, which use 4-wire active current loop interface are connected to the PTS controller through the HY interface converter. Examples of such dispensers is Hong Yang, others.
Electronic dispensers, which use 4-wire active current loop interface are connected to the PTS controller through the NP interface converter. Examples of such dispensers is Nuovo Pignone, others.
Electronic dispensers, which use RS-232 interface are connected to the PTS controller through the RS-485/RS-232 interface converter. Examples of such dispensers is Lanfeng, others.
Mechanical dispensers, which do not have electronic pumphead or interface for communication, can be connected to the PTS controller through the use RS-232 interface are connected to the PTS controller through the controller over mechanical fuel dispensers. Controller over mechanical fuel dispensers is intended to be used in connection with a control system for petrol station (POS system, cash register, OPT terminal, etc) to provide direct control over operation of electronic and mechanical fuel dispensers by controlling dispenser’s internal resources: motor, pulse sensor, nozzle, slowdown valve.
PTS controller converts a proprietary dispensers and ATG systems communication protocols into a single communication protocol, which is called UniPump. Thus using a single communication protocol UniPump a control system (POS system, cash register, payment terminal) is able to provide control over any of the supported dispensers and ATG systems in exactly the same way. For a developer it does not matter which brand or model of the dispenser or a POS system is connected - control over it through the PTS controller is done in exactly the same way.
PTS controller uses 12 V DC for feeding. Maximum current consumption is 400 mA.
Power supply source is not supplied together with a PTS controller. The power supply should be selected locally. This is connected with a reason that differennt countries may have different electricity network specifics: frequency and voltage.
At selection of the power supply you need to pay attention to the following 2 factors:
- output voltage of power supply should be 12 V DC
- maximum allowed current consumption of power supply should be more that maximum current consumption of PTS controller. If several devices are connected to the same power suource - then their total current consumption should be less than maximum allowed current consumption of power supply.
Connection of PTS controller to the control system (POS system, cash register, OPT terminal, etc) is made through a PC port of PTS controller, which has RS-232 interface (3 wires: TxD, RxD, Gnd). In case if the control system does not have a COM-port – it is possible to use any type of converter to COM-port (like USB-to-COM, Ethernet-to-COM, Bluetooth-to-COM, other converters).
NOTE! Some of the proposed USB-to-COM converter cables can bring problems when communicating with PTS controller. Reason of these problems is that since PTS controller uses quite high baud rate for communication (57600 baud), so some USB-to-COM interface converter an "eat" some of the transferred bytes in the communication exchange, so that the transferred messages will be incorrect and communication will be stopped or made incorrectly. That is why it is recommended to use USB-to-COM interface converters on the basis of FTDI chip (www.ftdichip.com), these converters are tested to have stable and correct communication with the PTS controller. Normally the COM-port adjustments window for this USB-to-COM interface converter looks as follows (screenshot is made in Russian language version of Windows OS):
Also a double-channel USB-to-COM interface converter on the basis of FTDI chip can be ordered directly from us, please see the product order code "USB-to-COM interface converter (2-channels)" here
Communication with PTS controller is made using commands and responses described in UniPump communication protocol. Thus PTS controller provides conversion of the common communication protocol UniPump into various proprietary communication protocols of fuel dispensers and ATG systems.
Yes, this is possible and PTS controller works on many petrol stations in exactly such a way.
This way of operation requires a control system to keep constant track over the dispenser state. Once the nozzle is taken up - the control system should authorize it with some volume, which is bigger than normal dispensing volume. After the dispensing is done - the control system should read transaction information from PTS controller and store its in its memory. As an example of such mode of operation please read how this is done in NaftaPOS software.
Communication with PTS controller is made using commands and responses described in UniPump communication protocol. Thus PTS controller provides conversion of the common communication protocol UniPump into various proprietary communication protocols of fuel dispensers and ATG systems. The set of instructions includes commands:
- Request status
- Authorize
- Suspend/resume dispensing
- Stop
- Get transaction information
- Get total counters
- Set/get prices
- Switch on/off the lights (present in some models)
- Get tag identifier (present in some models)
- Get ATG measurement data
PTS controller is supplied with full API (application programming interfaces) and open-source test applications for mostly used programming languages and operation platforms: C (for Windows and Linux OS), C++, C#, Delphi, Java, Python, Visual Basic, VB.NET, COM-object.
Yes, for each of the popular programming language we supply API and an open source applications for provision of control over dispensers and getting data from ATG systems. All software is given for free. You can use these application as a startup for your own POS system appilications and/or modify their source code to what is required by you.
Ask YOUR questions about
"PTS-1 controller over fuel dispensers and ATG systems"
Other products of section:
![]() |
U2L converter
U2L converter converts from IFSF protocol with LON interface to Tokheim UDC protocol with RS-485/RS-232 interface and backwards, it is intended for communication of POS systems and controller with dispensers, which use LON interface and IFSF protocol, through interfaces: RS-232, RS-485, RS-422.
![]() |
L2D converter
L2D converter converts from IFSF protocol with LON interface to any dispenser, which supports DART protocol with RS-485 interface and backwards. It allows POS systems and forecourt controllers, which use only IFSF-LON to communicate with any dispenser using DART communication protocol.